The mining industry is about to change a lot because of new technologies that allow mines to operate without people. Even though completely automatic mines might take a while to happen, there are steps being taken to use less human help underground. Mining companies everywhere are using robots and automation to make mining safer, more productive, and more efficient. However, switching to unmanned mines has its own difficulties.
This article takes a closer look at the roadmap for achieving unmanned mines. We discuss the technologies and strategies required to make this transition, as well as the infrastructural challenges that need to be overcome for seamless implementation. So let’s get started.
The Promise of Automation
For long, mining has been one of the most labor-intensive industrial sectors. As per industry reports, mining employs around 2% of the global workforce. The work environment deep underground entails significant health and safety risks for workers. The automation of mining processes carries the potential to create safer working conditions. These conditions can be made by removing humans from hazardous underground environments. So, robotic machinery and automated haulage trucks can take over risky tasks in underground tunnels, quarries, and more.
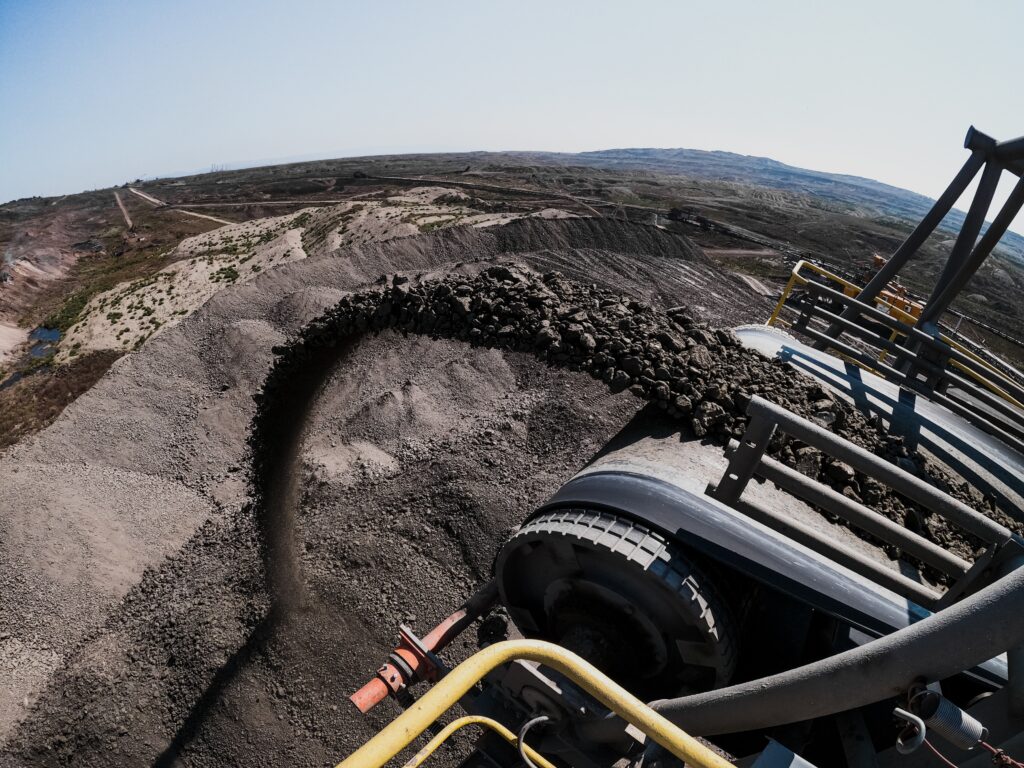
Unmanned mines also enable continuous productivity by reducing downtime and human errors. According to industry analysis, automated mine sites record 15-20% less downtime versus human-operated mines. Automated technologies also generate valuable data on various aspects of mining operations. Analytics based on this data further drives process optimizations and predictive maintenance. As a result, it lowers costs and minimizes unplanned outages.
Real-time remote monitoring and control of mining operations is also becoming viable. This is with improving sensor technologies and wireless coverage. As a result, the fusion of automation, connectivity, and data analytics paves the way for next-generation smart mines. These mines can set new benchmarks in operational efficiency.
Let us move ahead and see the technologies and strategies for unmanned mines along with their challenges.
Advancing Remote Control Centers
Remote control centers are special places where mining companies can manage their equipment without being on-site. Instead of being at the actual mine, people work from these centers, controlling driverless vehicles and robots using computers. They use dashboards to see what’s happening in the mines and make sure everything is running smoothly.
However, setting up these remote control centers for unmanned mines isn’t easy. There are challenges, like making sure there’s a good internet connection between the mines and the control centers. Cybersecurity is also crucial to protect these systems from hackers. Plus, the people working in these centers need proper training to control the machines effectively from a distance. Solving these problems is really important for making remote control centers work well.
Developing Robotic Mining Technologies
While driverless trucks and robotic LHDs are gaining adoption, automating many specialized mining tasks remains challenging. Ongoing R&D aims at creating robots designed for the rigors of underground environments. These robots for unmanned mines can take over intricate jobs. It includes tunneling, mineral extraction, and maintenance tasks.
However, robustness and flexibility remain key challenges in adopting specialized mining robots. Researchers are working on robust frames, seals, controls, and sensors that can withstand harsh conditions. Developing versatile robots that can be deployed for various jobs can maximize utility. Furthermore, researchers are prioritizing the advancement of battery technologies. It is to enable prolonged robotic operation underground for unmanned mines.
Automated haulage and transport
Driverless trucks and conveyors are taking over material transport and haulage roles in both surface and underground mines. Haul trucks operated by onboard computers and guidance systems can autonomously navigate along predefined routes. With no human driver, these trucks can operate continuously without breaks or distractions. Their routine operation generates massive amounts of data on metrics like fuel efficiency, maintenance needs, and more.
An autonomous haulage system can increase production annually while eliminating driver-related risks. Moreover, Conveyor systems transport broken ore and waste rock without needing human supervision. Automated haulage and transport technologies significantly improve safety. This is by removing workers from hazard zones. These techs for unmanned mines also optimize operational efficiency through uninterrupted productivity and data-driven improvements.
Autonomous drilling and blasting
Special machines called automated drilling rigs can drill holes in the ground all by themselves. These machines are very smart. They use computer controls, GPS, and sensors to figure out where to drill. They can even tell if the ground changes and adjust how they drill. No humans need to help them. After the drilling is done, explosives are put into the holes using remote control. These explosives are set to explode only after everyone is safely away from the area. This means workers don’t have to handle explosives directly.
Using these smart machines for drilling and blasting is safer because workers don’t have to do these risky jobs. Also, because the machines are so precise, they create holes that are always the same, which is really important in mining. In the future, experts can use the data from these machines. This is to improve drilling and blasting techniques further for unmanned mines.
Building Connected, Automated Mine Infrastructure
Transitioning to driverless vehicles is just one element of creating an unmanned mine. Upgrade the surrounding infrastructure with smart systems and connectivity. It is to enable smooth autonomous operations.
Most existing mines were built decades ago without advanced technological capabilities. Integrating modern communication networks, sensors, and automation into dated infrastructure poses challenges. So, a mine first needs to invest in improving wireless connectivity, likely 4G or 5G networks. It helps to allow vehicles, systems, and edge devices to reliably communicate data across the site.
Sensors like LIDAR, cameras, and IoT devices will then be incorporated throughout the site. It is to collect and relay key data on vehicle locations, road conditions, equipment health, and more. Control centers can monitor this flood of real-time data. It is to coordinate traffic, identify problems, and also make operational changes.
The road ahead
The mining industry is gearing up for radical changes. These changes are driven by automation, connectivity, and electrification. While fully autonomous mines may still be distant, early strides in unmanned mines show promise. However, realizing this vision requires a measured, phased approach accounting for varied challenges.
People will continue to drive sustainable success through creativity, collaboration, and technology leadership. This is even when unmanned mines may have no human presence underground. So, the road ahead promises exciting progress in mining 4.0 through human-machine convergence. Moreover, with responsible execution, the mining industry can usher in a new era. It can be an era of optimized performance and minimal risk.
If you want to be a step ahead in your industry and implement these futuristic changes, make sure you attend the 3rd Mining 4.0 summit. It will take place on 9-10th November 2023 in Barcelona, Spain. It will shed light on the challenges and opportunities mining 4.0 presents with automation, decarbonization, robotics, and more. Moreover, the presence of industry leaders and revolutionists will provide a great networking opportunity as well.