The mining and metals industry is in a unique position. The world moves towards decarbonization and limiting GHG emissions, but the demand for metals is growing. Decarbonization without electrification appears impossible. Electrification needs copious amounts of metals and minerals. As a result, the mining industry needs to seek out ways to increase efficiency while still limiting its carbon footprint. Enter digitalisation. Modern innovations in AI and general digital technology can now allow mines to upgrade their efficiency without major equipment overhauls. So let’s take a closer look at some of the technologies helping miners today.
Automation
While not as widely publicized as self-driving cars, the mining industry has actually been at the forefront of vehicle automation. For example, since the early 2000s, mines around the world have benefited from self-driving trucks, loaders, haulers, and other vehicles. The benefits are clear, automated vehicles are safer and more efficient than their human-driven equivalents. The AI that guides, for example, an excavator can predict and choose the most fuel-efficient route whenever it moves. As wireless technology has developed, particularly with new 5G networks, mining operations are able to expand their automated fleets. This helps offset the risks of labor shortages, as an automated mine does not need as many workers.
Digital twins
A digital twin is a computer model of the mine and its materials. This technology allows workers to remotely monitor the entire system. They can gather large amounts of data about the mine, from gross daily output to the status of individual valves, to help them plan daily operations. Digital twin technology also allows industry leaders to benefit from advancements in artificial intelligence (AI) technology. An AI can evaluate long and short-term data to show a company ways it can improve efficiency and productivity. A digital twin complements this point by allowing new employees to familiarise themselves more with an operation. This technology can also be integrated with blast measurement technology. Modern mining techniques now allow operators to predict how and where ore and stone will fall during blasting. This has the two-fold benefit of bolstering safety and increasing productivity.
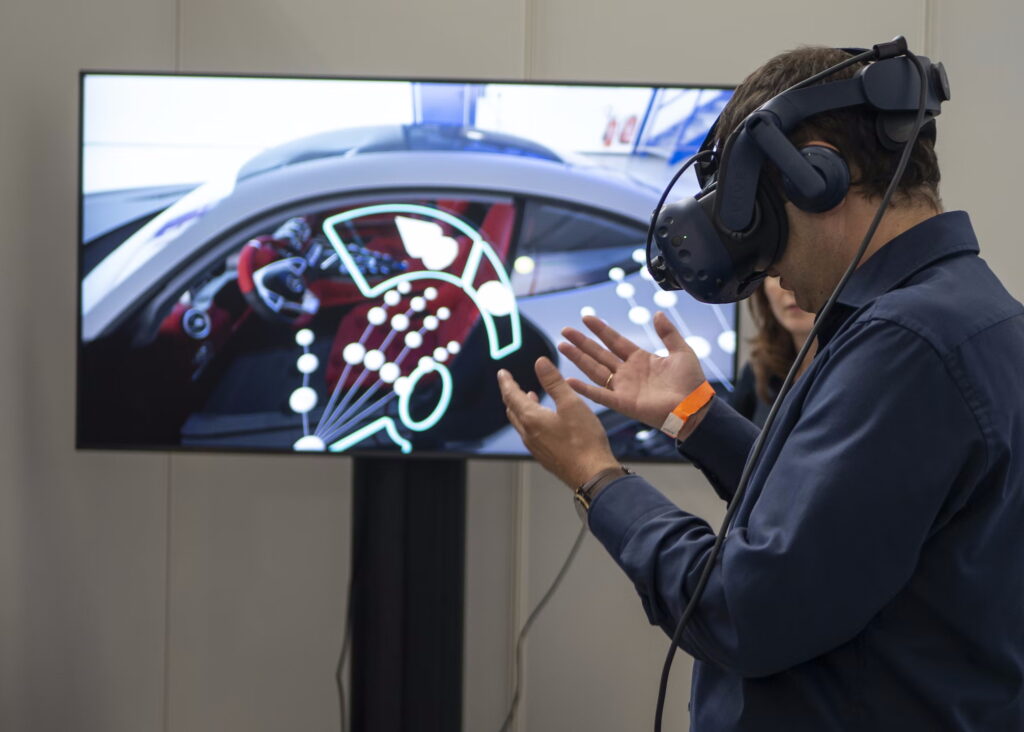
AR
Like digital twins, augmented reality (AR) allows anyone with the necessary hardware to visit a mine. This seems like a simple way to familiarise new staff with the operation. However, there are other benefits to AR. Workers in the mine can get instructions and other vital information directly in their AR glasses. This benefits both their effectiveness and safety: they gain increased situational awareness, which is vital in a busy environment like a mine. It also saves miners time as they do not have to pause what they are doing to check environmental data and watches. AR can also allow engineers to develop expansion plans remotely, which helps efficiency and drives down costs.
Workforce training
As the mining industry develops new technologies, it faces the challenge of getting enough skilled workers. Experts see workforce retention and training as the second largest risk area for mining. Mines need workers with technical skills in AI, sustainable energy, and automation to compete with other fields for new talent. Labor shortages are compounded by the steadily rising costs of training. Digitalization can offset some of these risks by reducing the amount of personnel required to run a mine. Similarly, digital skills can be acquired remotely, which would allow a company to reduce training costs. Retraining also benefits from remote skills training. Workers in mine A do not have to travel to a third location to prepare for work in mine B.
What can companies do now?
The mining industry is well-positioned to take advantage of recent innovations in wireless networks and artificial intelligence. Digitalization can mean a new era of high-efficiency mining if implemented correctly. Mining companies should conduct a comprehensive assessment of their facilities and equipment to find areas where digital technology can help. Companies should investigate how other mines have started to overhaul their technology, and learn from those experiences. Different situations require different solutions and paths; therefore, learning from others is a smart way to avoid any potential pitfalls. Join key decision makers at the 2nd Energy Transition for the Metals and Mining Industry conference, on January 19-20th, in Toronto, Canada. Industry leaders will gather to discuss and exchange the best practices for implementing green fuel and sustainable infrastructure. Visit future-bridge.eu or follow us on our social media to keep track of other events about sustainability in the mining and metals industry.